Technical Bulletins Archive
Filter by Year
- 2023 2
- 2022 1
- 2021 4
- 2020 1
- 2019 2
- 2018 1
ISO9001:2008 Approval for Bellis Technology China
2014 has been a great year for ITL and our wholly owned manufacturing plant, Bellis Technology Ltd (China), with our strongest year to date.
Due to the volume of orders being processed and built at our China factory, it became necessary to increase capacity, this came in the form of a 2,500m² factory expansion that was completed earlier in the year, paving the way for increased production.
In November, Bellis Technology received ISO9001:2008 quality management certification. ISO 9001:2008 sets out the criteria for a quality management system and is the only standard that can be certified to. This standard is based on a number of quality management principles including a strong customer focus, the motivation and implication of top management, the process approach and continual improvement.
The ISO project team was created in February with a goal of achieving accreditation by the end of December. The team consisting of five colleagues from China and one from the UK, worked incredibly hard and gained the accreditation by November, a great achievement for all in the ITL group.
Earlier in the year, we also obtained UL approval for our NV200 and SMART Payout. To obtain UL classification we had to demonstrate our ability to produce a product that complies with all of UL’s strict requirements including; casualty, fire & shock risks and other UL regulatory codes. UL is a globally recognised standard but is of particular importance in North America. By achieving this rating we can take steps to further improve our market share in the US.
During a visit to our Head Office, staff from our manufacturing facility in China; were in discussions with UK colleagues, regarding further development and build of new products to be manufactured in China next year. The teams are also investigating ways to improve material flow, production yield and factory automation, not only to sustain our new accreditations but also to continually innovate and improve upon our products.
The accreditations acquired this year are significant to both BTC and ITL as a group, as this means more tough regulations and further control on the quality of build ensuring we continue to strive for the best product reliability in the market. Not only do we believe as a group that our products are of the highest standard, we also now have the accreditations to prove it.
Operations Director, TJ Crowley said, “The achievement by the Quality team at BTC to attain ISO9001:2008 approval status is a significant milestone in the development of our facility in Shenzhen. The dedication of the team at BTC on this project ensures that we can assemble and deliver products to our distribution hub in Oldham that will meet the high quality and reliability standards necessary for our global customers.
We aim to further enhance our reputation for excellence and to meet the goals we have set for ourselves - to create a culture within BTC that will make it a World class manufacturing enterprise.
I am incredibly proud of the project team, YuKi Yao, Jason Guo, Annie Zhang, Hellen Huang, Michelle Xie, Stanley Li, Denis Lee, Alex Zhou, Annie Yang, Frank Xiong, Leo Cai and Ken Wang, all under the strong jurisdiction of factory manager, Ivan Ji. Not only did they achieve the ISO accreditation, but they also gained it earlier than anticipated, a huge achievement for ITL and BTC”..
The Graduate Adventure - Part 2
I have been working at ITL for almost six months now and am gradually getting to grips with all aspects of the marketing that we undertake. Next year, I am looking forward to making a real contribution to ITL’s global marketing strategy for 2015.
As we are an international company, we have customers all over the world and due to final posting deadlines, Christmas cards are thought about very early. This year, Dayna and I decided that I would attempt to create a Christmas card bespoke to ITL. A few alternative designs were created; you can see the actual card we sent out here.
The coming three months are our busiest time of year with preparations for the London exhibitions well under way and the exhibitions themselves taking place upon our return from the Christmas break.
As a global and ever expanding organisation, it is incredibly important for ITL that we have a presence at exhibitions as it allows us to communicate with both customers and stakeholders all under one roof as well as showing our existing product range and launching our innovative new products.
With the first exhibition taking part in January, the stand design has been my main priority. I was provided with a scale drawing of our 9×9.5m² stand by our stand builder. I spent time honing my Photoshop skills and worked with our stand builders to create the perfect stand layout.
I am really looking forward to visiting these shows for the first time and will let you know in our next blog how they all went. Fingers crossed the stand design is our best yet!
Mia Harding, Graduate Marketing Assistant
Over the past 6 months, since joining ITL at the end of June, I have been working within a team designing the next generation banknote validators.
My first major task on the project was to define new components on internal systems. I have had to familiarise myself with a few of the systems used at ITL; Teamcenter, PADs and Live Part Library to name a few. Although new to me, it was quite an easy learning curve as I have used similar programs during University and at my previous job.
I have also worked closely with the team leader (John Tillson) in developing the circuit diagram which was later put together in an internal system. Presently I am almost half way through developing the PCB layout; this has been ongoing for the past couple of weeks since the completion of the circuit diagram.
My MSc program was based on Electronic product development and this project is helping me to put into practice the skills gained from University. Of course there are more real world challenges here, but the MSc program helped me to be more prepared for these various challenges.
Jean Gilbert Nzeye, Graduate Electronics Design Engineer
Over the past month I have been providing technical assistance to our operations department in the production of a brand new product that is yet to be released.
I have gained valuable knowledge of the product through exposure to the assembly and repair of units, something that has been very useful as recently I have been fault finding and identifying where improvements might be made in the production process.
Seeing the production of the units has shown me how products are designed for easy assembly and where it is appropriate to use certain design features.
At the moment I am part of a team designing and prototyping the next generation of ITL’s cash handling products. I designed the mechanical components of the product using 3D CAD software and produced a prototype shortly after using the 3D printer in our onsite workshop.
I am looking forward to working with electronic and software engineers to develop the product further and provide solutions to any mechanical problems that might arise.
Michael Tillson, Graduate Design Engineer
InnoPrint - alternative ticketing solutions
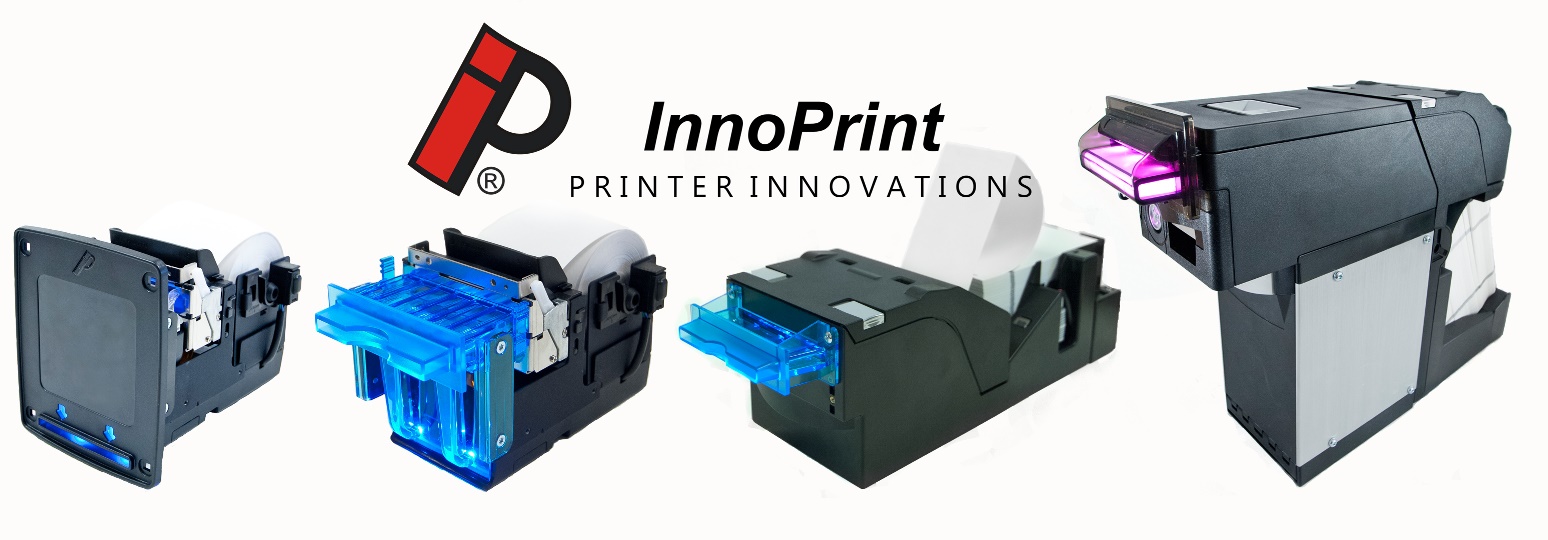
A successful year for the ITL Sales Team
Last week saw the ITL Group Sales Team from across the globe gather to discuss this year’s performance and their plans for the coming year.
18 staff from 7 worldwide office locations convened at their head office in Oldham for the two day event featuring members of both Innovative Technology and InnoPrint’s Sales Teams.
The annual sales event was a huge success commending each member for their input to ITL’s greatest year yet, with record breaking sales and unprecedented growth in all areas of the business.
All members of the team returned home, having celebrated Christmas with their colleagues, with a heightened sense of determination and morale for the exciting year ahead.
Merry Christmas
Season's Greetings from Innovative Technology. Best wishes for Christmas and a prosperous New Year!
Please note our European offices will close Wed 24th Dec and re-open Mon 5th Jan 2015. If you need assistance during the holidays please email This email address is being protected from spambots. You need JavaScript enabled to view it. and we will try to get back to you as soon as possible.
Innovative Technology present new printing products at EAG stand 910
December 2014 Technical Bulletin - Innovative Technology
IN THIS BULLETIN: Validator Manager 4.3.3, SSP Manual Update 2.2.0, MDB now available for recyclers, NV9USB+ Release, Upcoming Exhibitions, SMART Hopper - Product Change Notification; Labels
Software
Software Download
We have various free software tools to help update our validator range.
Please click below to access the latest version and always ensure you are using the most up-to-date issue before reprogramming.
If you cannot find the software you require please contact Technical Support:
E: This email address is being protected from spambots. You need JavaScript enabled to view it.
T: +44 161 507 1818
Title | Version File | |
---|---|---|
ITL Customer Software Guide (GA02037) | 1.2 | Download > |
Validator Manager | 5.1 | Download > |
DPS (Device Programming System) + DA3 | 1.2.6 | Download > |
NV Card Utilities | 1.9.21 | Download > |
ITL Drivers | 2.1 | Download > |
GBP SMART Update | 4.00.03 | Download > |
A month in the life of an ITL Customer Support Manager
Coming up to a year at ITL, Dan Humble, Customer Support Engineer, gives us an insight into working life at ITL.
The day to day role of a technical support engineer can vary drastically and you can be required to travel to the far corners of the earth at the drop of a hat, all to ensure our customers receive the best service possible.
The month started off with me preparing for a week in Barcelona, the aim of the visit was to train two new repair technicians at our Spanish office. It is always good to spend time with our overseas colleagues who we do not get to see every day. This was my second trip to the Spanish office in as many months and it went very much like the first; long working hours during the day, followed by relaxing alongside my Spanish colleague with a few beers in the evening!
After a successful week of training and siestas I returned to the UK for no longer than a couple of days, before a trip to Colombia was on the cards. A few days and a 17 hour flight later, I landed in Bogota for the very first time. Again, the main focal point of the week was product training and definitely not the local export! The customer really appreciated the effort in travelling over to visit them which is always great to hear – they even took me to the Museum of Gold!
Another 17 hour flight and I was finally home – ready to spend a few nights in my own bed before rounding the month off with a day in exotic…..Wales – this time for a catch up meeting with a customer. Visiting our customers gives us a great opportunity to discuss outstanding issues whilst also building relationships with them face to face.
As an international company, we have customers all over the world and being part of the support team, you have to be ready to travel to any one of these locations… even if that means Stamford Bridge (I’m an Arsenal fan) – the location for the London Autumn CoinOp show. I travelled down to London with the UK Sales team a day before the show, to help set up the stand and the products we were exhibiting.
This just details a few examples of a wide range of duties that support engineers at ITL fill on a day to day basis. With Innovative Technology growing at the current rate, it is only going to get busier! Who knows where support will be in the near future; seeing as we have just recruited an Australian Sales director, I know where I have my eye on.